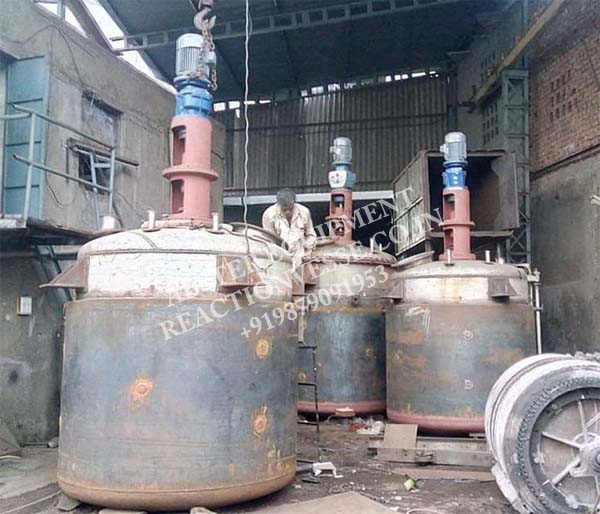
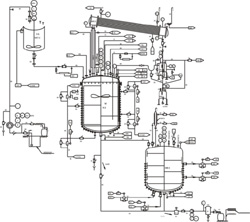
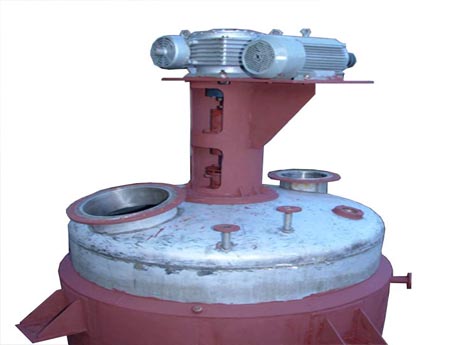
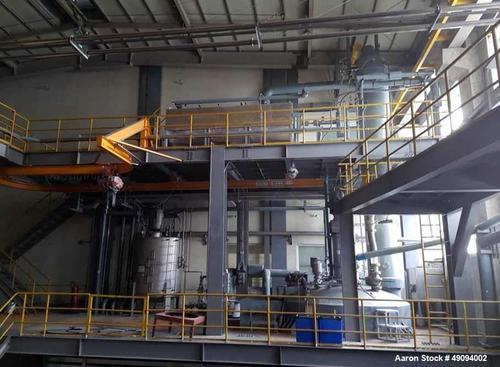
Unsaturated Polyester Resin Tank
Abster make Unsaturated Polyester Resin Tank is developed and supplied as per our clients' requirements. The basic system consists of a reaction kettle, vertical column, sub-cooler, and horizontally inclined condenser with separator and dilution blender. The batch time is approximately 16 to 20 hours and therefore, suitable mechanical seal arrangement for better results and to prevent any leakage is provided.
Abster Equipment engaged in manufacturing and exporting Unsaturated Polyester Resin Plant our clients spread worldwide. We Manufacture resin plant from 50 liters to 20 tons, batch on solid base. Polyester Resin Plant is available in various technical specifications are appreciated worldwide for its unique features such as high durability, corrosion resistance and optimum utility. In resin plant we provide Limpet coil reactor , packed columns, Shell and Tube Condenser , separator and blender ,if need then we provide internal cooling coil ,in reactor heating temperature range 50 to 250 degree by thermic fluid heater , condenser tube side row material of resin and shell side water for cooling purpose, column inside ss strap and ceramic for material back to reactor ,column outside water circulation line , separator capacity depend on reactor volume ,when heating & mixing is completed then transfer material in blender for temperature cool down purpose , when material temperature around 30 to 50 degree material move in packing drum
Abster is leading manufacturer of Polyester Resin Plant. There are two types of Polyester resin, Saturated & Unsaturated Polyester resin. Saturated Polyester resin is used in Pigment, Ink, Coil Coating, Thermo Plast, Soda Bottle, Textiles, X-ray films, Magnetic tapes, Packaging , Metalized film. Unsaturated Polyester resin is widely used in Sanitary-ware, pipes, tanks, gratings and high performance components for the marine and automotive industry. The Major Operations involved in the manufacture of polyester resin are etherification and blending – which are carried in their respective kettles. The most common raw materials used are polypropylene glycol, melic anhydride and styrene monomer. In addition small quantities of inhibitors and additives are required for the process.
The Process involves is poly Condensation reaction and blending the polyester resign with monomer. Due to the sensitive of polyester resign to contamination
The esterfication reactor is changed through a manhole with required amount of glycol and the solid anhydride. The mass is heated up to 200°C under agitation and inert gas N2 is slowly applied. The partial condenser condenses the glycol but process the water to the total condenser. The esterification is continued until a predetermined acid value 10 to 15 is reached. After achieving the predetermined viscosity the heating is stopped and the batch is dropped in to the blending kettle. In the blending kettle the batch is cooled to 100 – 102°. Styrene is pumped in the blender and viscosity is adjusted until the batch attains room temperature. The batch is then pumped through filter in to the storage tanks.
Unsaturated Polyester Resin Tank SPECIFICATION
Capacity | 50 L TO 20,000 LITER |
Machinery in Plant | Chemical Reactor , Column , Condenser , Receiver & blender |
Reactor Type | Both Dish End , Motor and Gear box , Inside Agitator for Mixing Material , Bottom discharge connection Vertical outer heating limpet and jacketed |
Usage/Application | Reaction , Mixing or Blending Row Material |
Mixing Material | Chemicals / Oils / Lubricant / Liquid Syrup / Sugar Syrup / Wax Melting /Engine Oil |
Material of Construction | Stainless Steel ,Mild Storage |
Orientation | Vertical Orientation |
Shape | Round |
Tank Diameter | As Per Your Requirement |
Electric Heater | Single Phase or Three Phase |
Temperature Controller | Automatic or PLC Operated |
Mixing Speed (RPM) | Variable , Speed Up And Down As Per Requirement |
Finishing Type | Matt Type ,Mirror Finishing |
Heating and Cooling System | YES |
Temperatures Range | 30 TO 250 Degree |
Vacuum | Yes |
Cooling Coil | Internal Coil |
Outer | Heating coil or jacket |
Plat Foam | Mild Steel |
Application Industry
- Pharmaceutical industry
- Chemical industry
- Food and beverages industry
- Petro-chemical industry
- Resins industry
- Polymers industry
- Coatings industry
- Adhesives industry
- Agricultural industry
- General chemicals industry
- Plastics industry
- Rubber industry
- Herbal Extractor
Resin Plants Technical Parameter:
Reaction Pot | Vertical Fractionating column | Horizontal Condenser | Separator | ||||
Specification(L) | Size of Fractionating column(mm) | Stuff Volume (m3) |
Cooling Area (m2) |
Specification (mm) |
Condensation Area (m2) |
Specification (mm) |
Volume (L) |
300L | Φ159×560 | 0.01 | 0.22 | Φ219×1000 | 2.4 | Φ410×450 | 60 |
500L | Φ159×750 | 0.015 | 0.29 | Φ219×1500 | 3.6 | Φ410×450 | 60 |
1000L | Φ194×800 | 0.025 | 0.62 | Φ273×1500 | 5 | Φ410×450 | 60 |
1500L | Φ194×850 | 0.025 | 0.62 | Φ273×2000 | 6.5 | Φ410×450 | 60 |
2000L | Φ219×1000 | 0.035 | 1.0 | Φ325×2000 | 8 | Φ600×600 | 150 |
3000L | Φ273×1100 | 0.058 | 1.2 | Φ325×2000 | 10 | Φ600×600 | 150 |
5000L | Φ273×1200 | 0.065 | 1.5 | Φ377×2000 | 15 | Φ700×750 | 300 |
8000L | Φ325×1500 | 0.065 | 4 | Φ426×2000 | 20 | Φ700×750 | 300 |
10000L | Φ325×1800 | 0.07 | 5 | Φ426×3000 | 30 | Φ700×750 | 300 |
15000L | Φ377×1800 | 0.08 | 6 | Φ450×3000 | 40 | Φ800×750 | 500 |
20000L | Φ377×1800 | 0.08 | 6 | Φ450×3000 | 50 | Φ800×750 | 500 |
25000L | Φ377×2000 | 0.12 | 10 | Φ455×3000 | 60 | Φ800×750 | 500 |
30000L | Φ377×2000 | 0.12 | 10 | Φ475×3000 | 80 | Φ800×750 | 500 |